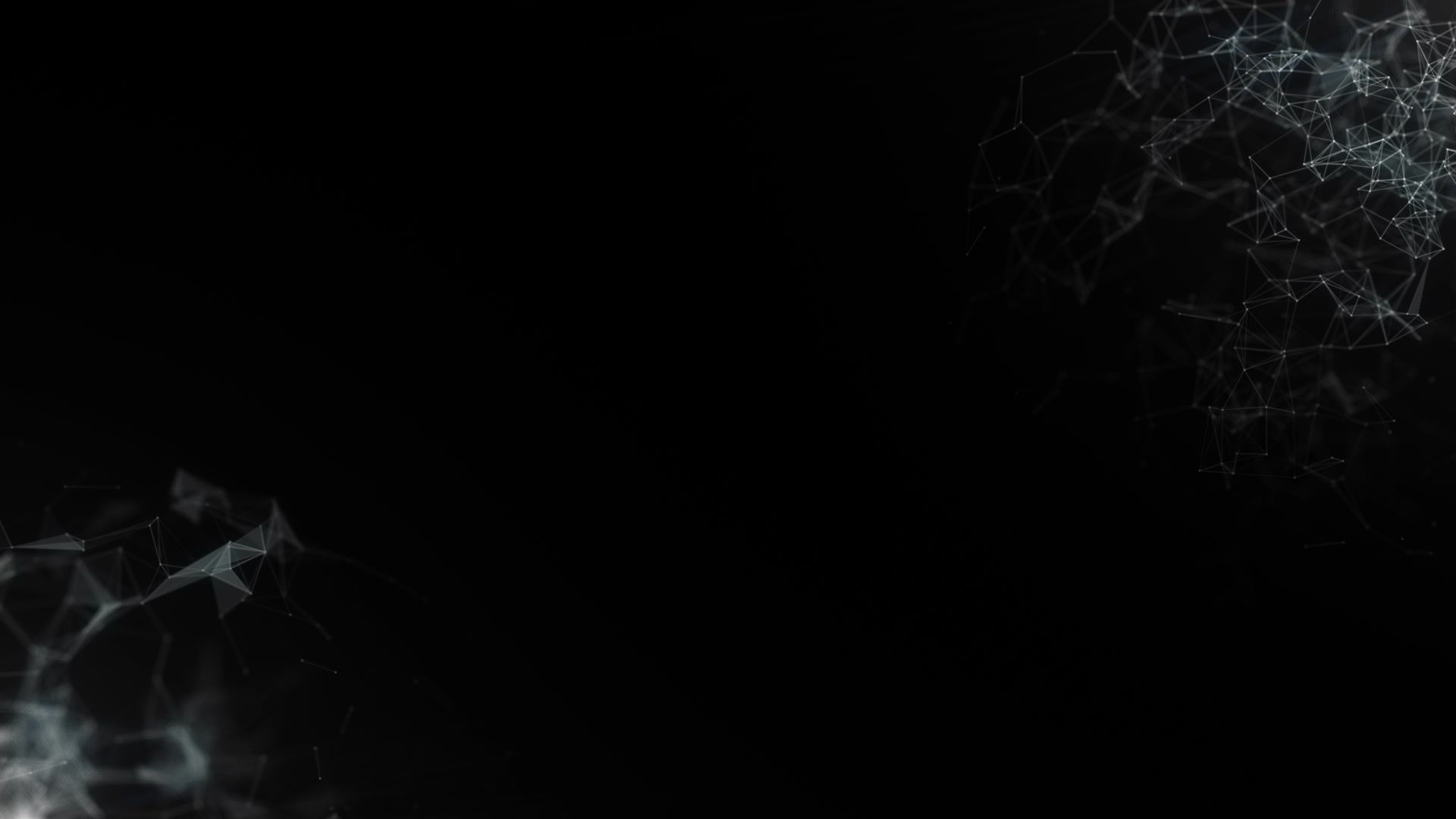
Dissertation Research
My dissertation research focused on the development of a patient-specific porous Poly(para-phenylene) (PPP) lumbar interbody fusion cage for spinal fusion procedures.
​
PPP is the stiffest and strongest unreinforced polymer available commercially, which allows us to introduce significant porosity in the material without sacrificing mechanical integrity. Ultimately the purpose of my dissertation research is to assess the viability of a spinal device made from this material which can be customized to individual patients by varying the porosity to match the strength of that patient's vertebra.
​
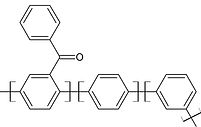
To better understand the mechanical properties of the vertebra, it was necessary to determine how the stiffness and modulus of the vertebral endplate varies with bone mineral density, endplate thickness, age, and other demographic and radiographic measures. The first portion of my research focused on developing predictive models for endplate properties based on these measures. This study was the first to calculate the modulus of the endplate, allowing for direct comparison of the endplate material properties to those of traditional engineering materials.
​

We developed a predictive model which allowed for accurate estimation of endplate stiffness and hardness from demographic and radiographic data. We also found that current materials such as PEEK and titanium are much stiffer than even the strongest endplates, indicating there needs to be some change in the design process for implants.

Next I built a finite element model to estimate the pushout force of PPP implants in-vivo. Initially, it was found that PPP allowed for significantly more bone ingrowth compared to PEEK implants, leading to a much higher pushout force. Also I analyzed the stress-dissipation behavior of porous and solid PPP and PEEK implants and found that they show the same stress dissipation response. More importantly, this model showed a behavior in both porous implants that cannot be captured by solid implants as shown below. Both porous material dissipate significant amounts of stress within the first millimeter of material while solid implants will directly transfer the load through showing a fundamentally different behavior which cannot be captured by solid materials.

Based off of the results seen in the first study, I built a finite element model which utilized the directly measured modulus values from the endplate. This study analyzed the interaction between various implant design parameters such as total implant contact area, endplate conformation, as well as material variation for patient-specific implants to evaluate the best method to reduce endplate stresses to prevent subsidence. Traditional design implants were compared to those which are conformed to the endplate as well as those which maximize the overall contact surface. It was found that there was little effect when reducing the modulus of the implant through porosity. Contact area due to conformation to the endplate showed much more impact to the endplate stresses. With this in mind, future implant designs should focus on providing some sort of contoured surface to contact the endplate.

